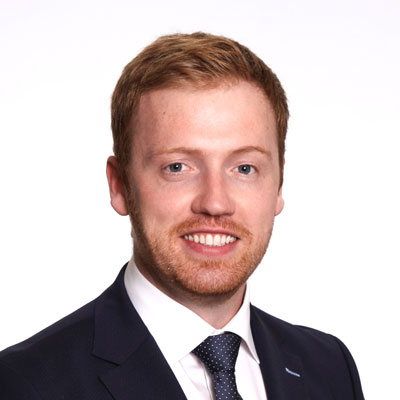
Seán McMahon, PhD
Global Business Manager, Bioresorbable Polymers, Life Sciences, Ashland
Bioresorbable polymers are critical to patient care, enabling long-acting injectables that provide extended-release of medication. These help boost therapy compliance, enhance therapeutic efficacy and reduce dosing frequency requirements.
Ashland ViatelTM bioresorbable polymers play a crucial role in the fabrication of degradable medical devices, including sutures, orthopaedic implants and biodegradable ‘scaffolds’ for cell growth to regenerate tissue.
Emerging centre for bioresorbable polymers
Ashland, a global additives and specialty ingredients company, has launched seven innovative technology platforms including this bioresorbable polymers platform. The company is supporting substantial market growth via the recently expanded facility located in Mullingar’s National Science Park, a biomedical hub.
“Our scientists carefully tune bioresorbable polymers for desired performance in terms of degradation and physical properties, creating huge application potential across the medical field from enhancing treatment of chronic diseases to supporting a new age of tissue regeneration. The Mullingar site is pivotal for developing and manufacturing these materials,” says Seán McMahon, Ph.D., global business manager.
Our scientists carefully tune bioresorbable
polymers for desired performance in terms
of degradation and physical properties.
Long-acting function
McMahon explains: “One way our pharma customers use our bioresorbable polymers is to incorporate a drug compound into the polymer to form a long-acting drug depot. The depot is injected into patients and safely biodegrades while slowly releasing the drug over a programmed duration, such as one to six months.”
This is particularly relevant to serious chronic illnesses that remain the leading cause of death in many countries. These depots reduce injection frequency and help patients stay in compliance to realise greater treatment benefits.
Embracing diversity
Focusing on precision chemistry, the solvers in Mullingar produce, purify and test polymers helping ensure quality and control. These chemistries offer great potential to solve some of medicine’s most complex delivery needs, including new routes of administration, tissue targeting and cellular delivery. “Custom polymer synthesis is probably the site’s most strategic capability because drug formulators are facing new excipient needs,” concludes McMahon.
Ashland has expanded its team by tapping into Ireland’s biomedical talent pool, and the Mullingar location is central to achieving the expansion. The facility has a fantastic workplace culture driven by a dynamic diverse team of people recruited globally.